🚲🚲: Maßgeschneidert automatisiert fertigen, an der Fachhochschule Südwestfalen / FH SWF
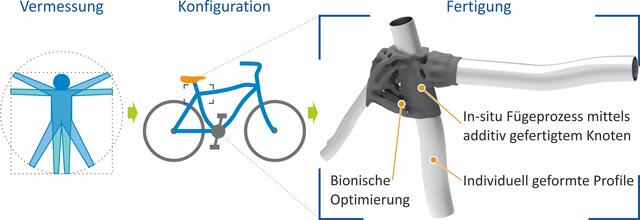
- Fertigung eines kundenindividuellen Fahrrads in Leichtbauweise. Quelle: Prof. Dr. Jörg Kolbe, FH SWF Meschede. Link: https://www.fh-swf.de/de/ueber_uns/standorte_4/meschede_4/fb_iw/dozentinnen/professorinnen_1/kolbe/index.php
- hochgeladen von Reinhard's BLOG: Viel, sicher(er) radfahren!
Forschung.
Individuelle Fahrräder mit CPS: Customized Production System
Meschede. Ein Team der Fachhochschule Südwestfalen arbeitet im Projekt Customized Production System an der Herstellung kundenindividueller Produkte in Leichtbauweise. Das Versuchsobjekt ist ein voll automatisiert gefertigtes Fahrrad. Denkbar sind aber auch Anwendungen wie beispielsweise Medizinprodukte.
3D-Druck
Gleich ob E-Bike oder Beinprothese: Die Produkte sollen in einer Kombination aus Umformtechnik und 3D-Druck hergestellt werden. Für das Demonstrationsobjekt Fahrrad bedeutet dies, der Rahmen wird aus gebogenen Rohren und bionisch optimierten, 3D-gedruckten Verbindungsknoten hergestellt. Und zwar gleichsam maßgeschneidert, das heißt individuell auf Größe und Gewicht des Fahrers oder der Fahrerin abgestimmt. „Die Produkte die wir herstellen wollen, sollen grundsätzlich leicht, groß und belastbar sein“, erklärt Projektleiter Prof. Dr. Jörg Kolbe, „deshalb haben wir uns für das Testobjekt Fahrrad entschieden.“
Konstruktion als Zwilling
Im Konstruktions- und Produktionsprozess wird jeder Fahrradrahmen zunächst als sogenannter digitaler Zwilling angelegt. Dies ermöglicht einen vollautomatisierten Produktionsprozess, in dem zunächst die Rahmenprofile geformt werden. „Im Fügeprozess klebt dann ein Roboter mit 3D-Druckkopf den Rahmen quasi wie mit einer Heißklebepistole zusammen“, so Kolbe. Die Technik dazu ist komplex: Der Druckkopf muss sechsachsig geführt werden, um Kollisionen mit den Bauteilen zu vermeiden und die Druckschichten optimal an der Bauteilgeometrie auszurichten.
🚲-Rahmenfertigung - ganz ohne Schweißen
Gegenüber anderen Produktionsmethoden bietet das neu zu entwickelnde Verfahren einige Vorteile. So könnten Fahrräder oder Prothesen aus Aluminiumprofilen und Kunststoff kostengünstiger gefertigt werden als aus Kohlefaser. Für Medizinprodukte ergäben sich sinnvolle Anwendungen in Entwicklungs- oder Schwellenländern. Im Vergleich zu vollständig aus Kunststoff gedruckten Bauteilen schneidet die Multimaterial-Struktur aus Kunststoff und Metall vor allem in puncto Fertigungszeit, Belastbarkeit und Recyclingfähigkeit besser ab. „Und das Tolle ist, dass wir vollständig auf Schweißen verzichten und so besser hochfeste Aluminiumprofile einsetzen können“, erklärt Kolbe.
Forschung für die digitalisierte Lernfabrik
Motiviert ist das Forschungsvorhaben durch den Trend zu höherer Individualität bei Consumer- und Medizinprodukten. „Was Sinn macht“, meint Kolbe, „man muss nicht mehr produzieren, als wirklich gebraucht wird.“ Zwei Jahre läuft das vom Ministerium für Kultur und Wissenschaft des Landes NRW geförderte Projekt. Im interdisziplinären Team arbeiten Umformtechniker Prof. Dr. Matthias Hermes, Leichtbauspezialist Prof. Dr. Jörg Kolbe und Automatisierungsexperte Prof. Dr. Gerrit Pohlmann zusammen. Ihr Ziel ist es, die Grundlagen für weitere Forschungen zu schaffen - und für eine vollkommen digitalisierte Lernfabrik, die am Standort Meschede der Fachhochschule Südwestfalen entstehen soll.
Wissenschaftliche Ansprechpartner
Prof. Dr. Jörg Kolbe
Konstruktion und Leichtbau
Portrait auf dem Hochschulserver
Fachhochschule Südwestfalen
Fachbereich Ingenieur- und Wirtschaftswissenschaften
Lindenstr. 53
59872 Meschede
Quelle für den Bericht
(idw) Informationsdienst Wissenschaft
https://idw-online.de/de/news778198
Bürgerreporter:in:Reinhard's BLOG: Viel, sicher(er) radfahren! aus Langenhagen |
Kommentare
Sie möchten kommentieren?
Sie möchten zur Diskussion beitragen? Melden Sie sich an, um Kommentare zu verfassen.